Table of Contents
More Fulfillment Content
Get the latest e-commerce industry news, best practices, and product updates!
Table of Contents
More Inventory Content
Share This
Get the latest e-commerce industry news, best practices, and product updates!
Table of Contents
Share This
More Fulfillment Content
Get the latest e-commerce industry news, best practices, and product updates!
To gauge a company’s profitability, it is vital to determine the value at which it records inventories in its final accounting statements. This is where inventory valuation comes into play. In this article, we will discuss inventory valuation, the significance of inventory valuation, inventory management, inventory valuation methods and their comparison, challenges existing in inventory valuation, and other related aspects.
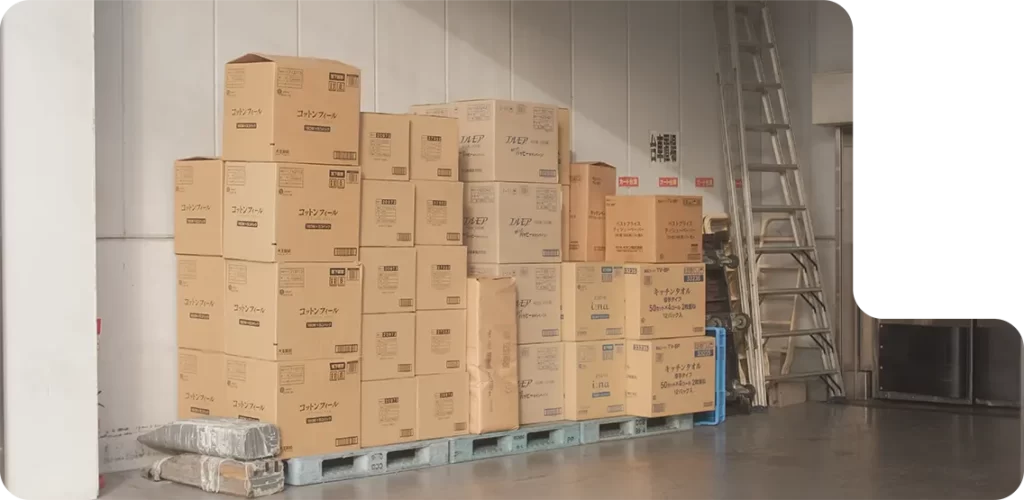
What Is Finished Goods Inventory?
Finished goods inventory is the total stock available in a company for sale to the customers. Customers purchase these products to fulfill their needs. Although, ‘finished goods’ is a subjective term that can have different meanings to different people or customers. This is because one person’s finished goods can be another person’s raw materials.
For example, textile manufacturing companies may produce many finished goods such as silk and cotton. They sell these products as finished goods, but purchasers, such as clothing retailers, buy these fabrics as raw materials. Clothing retailers then use silk and cotton to make desired garments. The seller mainly uses the finished goods inventory formula to calculate the value of their goods for sale.
How to Calculate Finished Goods Inventory in Manufacturing
Calculating finished goods inventory in manufacturing is very important to gauge your company’s finished goods inventory accurately. The calculation of finished goods inventory requires two main things: the cost of goods manufactured (COGM) and the cost of goods sold (COGS).
Thus, the formula for calculating the finished goods inventory is:
Finished goods inventory= (COGM-COGS)+ value of the previous year’s finished goods
Where, COGM= cost of goods manufactured
COGS= cost of goods sold
The formula for calculating COGM and COGS to help estimate the finished goods inventory is:
COGM= (Beginning WIP Inventory + Total Manufacturing Cost) – Ending WIP Inventory
COGS= (Beginning Inventory + Purchases During the Period) − Ending Inventory
Where, WIP= work in progress
We can simplify the calculation of finished goods inventory in these three steps:
- Step 1: Check your company’s previous year’s finished goods inventory record.
- Step 2: Subtract the current cost of goods sold (COGS) from the current cost of goods manufactured (COGM).
- Add the value of the previous finished goods inventory to the amount you received as an answer in step 2.
How to Calculate Beginning Inventory of Finished Goods
Beginning inventory is the value of a company’s goods at the start or beginning of an accounting period. Beginning inventory is a vital current asset in the accounting process. It is the inventory that a company can put up for sale to generate revenue.
All companies must calculate beginning inventory at the beginning of any accounting period.
The formula for calculating beginning inventory is:
Beginning inventory = COGS+ Ending inventory – Purchases
Where, COGS= cost of goods sold
To calculate the value of the cost of goods sold, you can refer to this particular formula:
COGS= (Previous accounting period beginning inventory + previous accounting period purchases) – previous accounting period ending inventory
Another aspect required for calculation is ending inventory. The formula for calculating ending inventory is:
Ending inventory = Previous accounting period beginning inventory + Net purchases for the month – COGS
Where, COGS= cost of goods sold
To make the process of calculating the beginning inventory easy, you may go through the following points:
- It is important to determine the value of the cost of goods sold using the records of your previous year’s accounting period.
- Multiply the balance of your ending inventory by the cost of production of every inventory item.
- You are required to follow the same process for the new inventory as well.
- Add the ending inventory and the cost of goods sold that will give you a certain value.
- Subtract the amount of purchase inventory from the value that has been received by following the above step.
What Is the Formula for Finished Goods Inventory?
Calculating the value of finished goods inventory requires a formula, just like any other calculation. Coming to a value of finished goods inventory helps a company estimate their sales and manufacture accurately.
The formula for calculating the finished goods inventory is:
Finished goods inventory= (COGM-COGS)+ value of the previous year’s finished goods
Where, COGM= cost of goods manufactured
COGS= cost of goods sold
Here is an example of calculating finished goods inventory to better understand the formula.
This is an example of a candle manufacturing store.
Step 1: At the end of last year, the candle manufacturing store had 800 finished candles in stock.
Candles cost Rs 10 each to produce.
Previous finished goods inventory value = 800 x 10 = Rs 8,000
Step 2: During the year, the candle manufacturing store made 1,000 candles and sold 700.
Cost of goods manufactured = 1,000 x Rs 10= Rs 10,000
Cost of goods sold = 700 x Rs 10 = Rs 7,000
Rs 10,000 – Rs 7,000 = Rs 3,000
Step 3: New finished goods Inventory= Rs 8,000+ Rs 3,000= Rs 11,000
Therefore, the formula for calculating finished goods inventory has been explained above with the help of an example.
Why Is the Finished Goods Inventory Formula So Important?
The formula for calculating finished goods inventory is critical for a company. It offers many benefits, but the chief advantage of calculating finished goods inventory is that it helps a company prevent stockouts and overstocking.
Below are the many advantages the finished goods inventory provides a company:
Helps To Identify Gross Profit
Inventory is one of a company’s most significant current assets, and finished goods inventory contributes to it. While preparing the company’s balance sheets, final accounts, and financial statements, it is imperative to note the value of the inventory. The inventory value is recorded when the amount of finished goods inventory is known. That is why it is essential to devise a formula to calculate the value of finished goods inventory that eventually helps identify the company’s gross profit.
Brings Out Accuracy In Current Assets
Inventory is a current asset for a company. Accuracy is necessary while calculating inventory to maintain an error-free accounting sheet. Even one mistake in the calculation can lead to a severe error in the audit. That is why the formula of finished goods inventory is necessary. It tracks the value of finished goods, works in progress, and raw materials as a part of the whole inventory.
Reduces Wastage Of Money And Materials
When you know the exact amount of finished goods inventory levels that you need to maintain in your warehouse, for the time being, it reduces the costs and waste for your company. Knowing your company’s optimal inventory value will help you overcome the problem of overstocking and stock-outs. Also, it will save the costs of acquiring massive warehouses and maintaining the present inventory.
Optimizes The Process Of Inventory Management
Various improvements and automation can optimize the process of inventory management. Knowing the formula for calculating finished goods inventory makes it easier for your company to calculate labor and manufacturing costs. It helps you to optimize the process of inventory management and increase efficiency.
What’s the Ideal Finished Goods Inventory?
There is no particular ideal finished goods inventory universally applicable for every company. But the concept of superior finished good inventory is quite simple.
An ideal finished good inventory prevents understocking and overstocking of products. If a company has a lot of overstocked products, then it is not an ideal finished goods inventory because of the tons of unsold inventory in the warehouse. That unsold inventory is hard to manage and look after in the warehouse and requires a larger space. Hence, a company shouldn’t have a lot of overstock finished goods inventory in their warehouse as it indicates the company is incapable of selling the products as much as they manufacture them.
Similarly, a company has a lot of under-stocked items, which is also not an ideal finished goods inventory. Such a scenario indicates that the company cannot supply its customers with the needs and wants of the purchasers. Stockouts show that customers are ready to buy the items but the company cannot fulfill orders as there is not much stock in the warehouse to address customer demands. This highlights the company’s inefficiency in catering to customer needs. Hence the scenario of stockouts is also not an ideal finished goods inventory. An ideal finished goods inventory is capable of avoiding both stockouts and overstocking.
Becoming Finished Goods Inventory
A product does not add up to finished goods inventory just like that. The process of becoming a finished good inventory goes through the stages of being a raw material first and then a work in progress, which eventually turns into a finished good that adds up to the amount of finished goods inventory.
The stages of becoming finished goods inventory are:
Raw Materials Inventory
Raw materials inventory is the total cost of products and items that have not yet been used as a work in progress or have not been converted into finished goods. Raw materials are further be divided into two categories as follows:
- Direct materials: These raw materials directly convert into finished goods, and there is no in-between. For example, a wardrobe is made using wood. In this case, wood is the direct raw materials
- Indirect materials: These raw materials do not directly convert into finished goods. These raw materials are consumed and incorporated while making the finished product, that is, in the production process. For example, a lubricant is an indirect raw material consumed in the production process of many finished goods.
In the case of accounting and preparing a balance sheet, raw materials are recorded as inventory assets that are a part of any company’s current assets.
Work in Progress Inventory
The intermediate stage of inventory is when the process of inventory has been started from the beginning as raw materials and is currently undergoing the development or assembly to turn it into a final product. Work in progress also refers to the labor costs, manufacturing costs, and other overhead costs that a company incurs in the production process. These costs are eventually transferred to the finished goods account and transferred to the cost of sales. The company eventually evaluates and earns these costs when the product is sold to customers.
Work in progress is recorded in the inventory asset account of a balance sheet as it is also a current asset.
Finished Goods Inventory
The total stock available in a company’s warehouse to be sold in the market is called finished goods inventory. It means no changes are required in the products before selling them to the customers, as they are the final products. Finished goods are recorded in the balance sheet as a part of the inventory account. Inventory is a part of the company’s current assets that are recorded in the company accounts.
Sign up today and leave the logistics to us
Sign up and we will get back to you within 24 hours to discuss what services would be best for your business needs. Or speak with us now and tell us what you need.
FAQs
The four inventory valuation methods are:
- Specific identification
- First-in, first-out (FIFO)
- Last-in, first-out (LIFO)
- Weighted-average
The two most common methods of inventory valuation are FIFO and LIFO.
FIFO (first-in, first-out) method assumes that goods are sold in the order they are purchased. It is an easy method for costing, which is extensively used.
LIFO (last-in, first-out) assumes that the newest stock is sold first. This method decreases the income tax affliction on the business. Moreover, it ensures that the company doesn’t face lower profitability.
Stock valuation is the process of finding out the theoretical value of a stock. Five methods of stock valuation are listed below:
- Dividend Discount Model (DDM)
- Discounted Cash Flow Model (DCF)
- Comparable Companies Analysis
- Asset-based Valuation Method
- Some of the Parts Valuation Method
When the matter comes to the selection of methods for inventory valuation, most businesses adopt the FIFO method. It is easy to use and presents the most precise value of profitability and cost. In addition to being easy to comprehend and easy to manage, it assists retailers in controlling spoiled and waste goods. This is because it always prioritizes selling the oldest inventory first.
In the majority of cases, businesses assume the inventory as an asset. The reason is the aspect on which the business spends money and its value. If it is being used by the company or sold as part of business conduits, they can consider it as an inventory. A company’s inventory can entail parts or segments of materials and products. Moreover, it also entails the finished products before shipping to sales and production items for sale.