Table of Contents
More Inventory Content
Share this
Subscribe to get the latest news!
Table of Contents
Share This
More Inventory Content
Subscribe to get the latest news!
Maintaining a company’s warehouse inventory levels is called inventory control, sometimes known as stock control. The inventory control procedure entails tracking products from when they’re ordered until their end destination or disposal. Over the years, several methods, techniques, and systems have been designed to aid firms in streamlining supply chain activities associated with inventory control systems. With the basic introduction out of the way, let us look at the importance of inventory control in e-commerce.
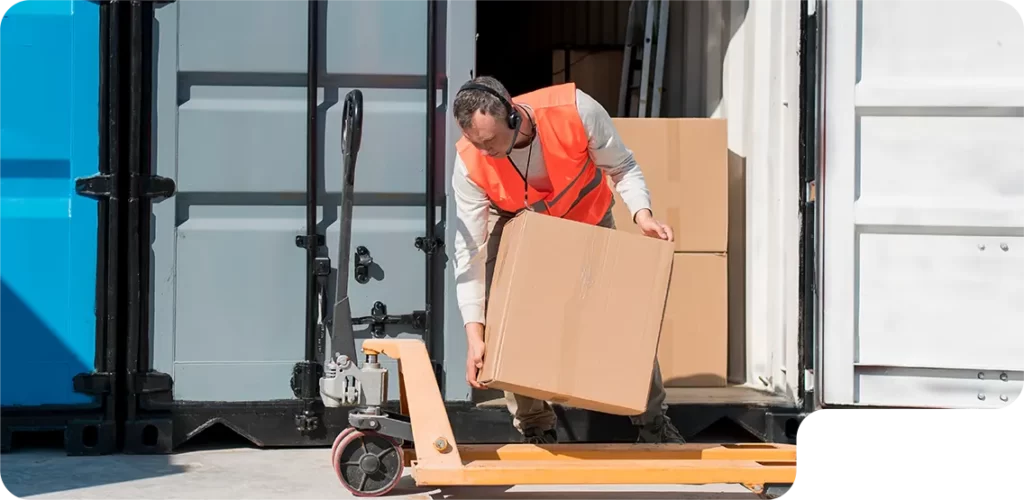
What Is Inventory Control?
Inventory control is the correct number of products or parts on hand to minimize shortages, overstocking, and other costly issues.
Inventory control reduces the quantity of slow-selling purchases made while raising the amount of high-selling items. As a result, inventory control keeps costs down for businesses since they don’t have to waste workforce reordering and receive things they don’t require. Furthermore, they avoid allocating valuable storage space to those goods, lowering carrying costs and making way for faster-selling items.
By employing inventory control, you may protect yourself from impulsive decisions and avoid the stress and money of overstocking goods. As the name implies, inventory control helps you keep track of your stock levels to make the most of your assets and avoid goods deterioration and expiration.
What Is Store Inventory Control?
Maintaining track of inventories across your retail locations is known as store inventory control. Store inventory control applies to both traditional and virtual retailers. It includes things from the first purchase to delivery to the retail outlet.
Store inventory control includes keeping track of inbound and outbound inventory and inventory maintained in the warehouses. Inventory control provides you with a comprehensive view of your firm’s operations, including what goods are in stock and where they are in the facility.
The idea is to cut down on the costs of holding onto goods. You’ll also know when to restock items, liquidate old stock, and purchase new things. Effective inventory control procedures will make more room in your warehouse and revenue in your cash inflows, ensuring you don’t maintain outdated or unsold stuff.
Inventory Control Vs. Inventory Management
Measures and activities aimed at managing and maintaining inventory demand and restocking are called inventory management.
On the other hand, inventory control is establishing and implementing procedures for managing inventories between the time it is acquired and the time it is processed into a finished product.
While inventory management entails keeping a list of when to restock, what to replenish, how much to produce, when to offload, and at what price to advertise, inventory control entails regulating stock in a storage facility, such as knowing what products are available, how many are usable, where they are located in the storage facility, and making sure the supplies stay in good condition.
What Is The Importance Of Inventory Control?
There is always the possibility of variations in material demand. However, if there are enough things in stock, you can control these variations. As a result, proper inventory control serves as protection from demand changes.
Some examples showcasing the importance of inventory control are as follows:
Reduces The Possibility Of Loss
Inventory control helps minimize the danger of missing items due to expiration (outdatedness) or degradation. It is because it frequently checks all of the things.
It also sells all slow-moving goods on time and at market rates. It only keeps the proper stock on hand at all times. As a result, the likelihood of any item becoming obsolete is lowered.
Working Capital Management That Works
Inventory control is essential for efficient use of cash reserves. It aids in the proper materials, parts, and other items on-site. It is not necessary to overstock. As a result, operating income will not be stifled by surplus inventory.
Ordering Is Not Duplicated
Inventory control prevents stock orders from being repeated. Controlling reordering is accomplished by keeping a distinct purchasing department. This unit will handle all of the organization’s purchases. Purchasing is not permitted in any other sector. As a result, there will be no stock ordering duplication.
Reduction In Order Cost
A company incurs some costs when it orders. Businesses must fill out various forms. Authorizations must be acquired, and products must be acknowledged, examined, and tallied when they arrive. The pricing will be determined by the number of purchases made. The less inventory there is, the less capital is required to carry it.
Creating An Effective Production Schedule
The production process can be done with poor, lengthy production models and planned timelines to achieve efficiencies and savings. Production planning becomes easier for administration when inventory levels are kept at a suitable level.
Avoiding Sales Loss
Without items on hand, most businesses would fail. Inventory control benefits both the enterprise and the consumer by assuring timely availability of a sufficient quantity of commodities. In theory, a company must be able to deliver things when requested.
Obtaining Price Reductions
When purchasing materials in bulk, many vendors may cut the price of materials and constituent parts. Large orders may enable the company to receive frequent rebates. These discounts lower the cost of items and improve profit margins.
Knowing When To Replenish Stockpiles
Inventory control necessitates keeping required records, which can aid in maintaining stocks within acceptable bounds. The corporation can defend itself from thefts, wastage, and inventory leaks by supporting sufficient documents. These statistics also help in the decision-making process for stock repurchases.
Protection Against Demand Fluctuations
A product’s demand projection is inaccurate in many instances. The demand projection and the actual market are always slightly different. However, there can sometimes be a significant gap between the projected and existing demand.
What are the Objectives of Inventory Control?
The objectives of inventory control are as follows:
- Because the inventory is kept in thousands of digits, it is necessary to keep storage and transport costs to a minimum. The expense of stock maintenance and storage is substantial in the firm.
- To supply goods, moving boxes, intermediate products, and other items needed to complete the order or meet the target within the estimated time frame.
- To minimize and efficiently control the inventory’s leftovers and non-moving goods.
- To take advantage of instances when inventory market prices are reduced and successfully manage stocks in the event of inflation when material prices rise, a store’s handling can be done far better and more efficiently.
- To effectively maintain reservoir and auto-continue minimum purchase quantity of inventories, among other things.
How Inventory Control Can Improve Your Business
There are various advantages to using an inventory system, which revolve around the efficient use of items. The rewards you receive will vary depending on the type of business you operate, its scale, and the kind of inventory you hold.
Some of the ways inventory control can improve your business are as follows:
Save Money On Storage
Inventory management systems assist in reducing expenses in other ways. If your company holds far more than it requires, storage, freezer, and employee salaries can mount up quickly.
Your organization can only maintain the ideal amount of goods in storage by offering projections of how much inventory you’ll need.
Boost Your Sales
An inventory control system can boost sales by lowering the possibility of being bought out of a product when a buyer wants to purchase it. You’re less likely to run out of popular items if you have a better grasp of inventory levels and how much you will sell.
Another advantage of having enough inventory is that your clients will get a more favorable impression of the business. Consumers are much less inclined to feel disappointed if an item they wish to purchase is unavailable.
Boost Your Productivity
Inventory control can boost efficiency by lowering the time spent maintaining inventories. Simple inventory control systems, such as excel spreadsheets, can help you retain track of the merchandise and make more intelligent choices faster.
Increases Client Happiness And Service
When clients inquire about specific items, effective inventory management means a supplier can rapidly determine availability. Consumers will have a better view of business due to the quick response times, and they will be less inclined to take their business to competitors. Well-organized inventory management enables producers to understand precisely the stock availability, allowing them to serve consumers more effectively and satisfying their customers.
Aids In Long-Term Planning
Inventory control is a valuable company asset that aids in task completion. A significant aspect that helps a company stay within expense is preparation. Keeping correct inventory records allows a producer to discover data and plan how to service-specific clients by recognizing what stock is available and when to order additional inventory.
Planning allows you to evaluate inventory data and gain a sense of patterns, making more educated restocking choices. A producer can better plan and inform their strategy if they keep this in mind. In addition, inventory management is crucial for significant investors and stakeholders who require strategic documentation for production processes.
Boosts Manufacturing Efficiency
Accurate inventory control can assist a manufacturer’s overall effectiveness. Instead of locating a particular piece of inventory, workers can dedicate their efforts to other duties. Employees can also be alerted when stock levels are shallow using warning thresholds.
Automation, which is a component of reasonable inventory control, means less time spent on time-consuming human involvement and much more time spent on other elements of the production operation. Automation improves efficiency, which has a direct influence on the company.
How To Avoid Dead Stock?
Here are some best practices you can adopt to prevent inventory from piling up and becoming a liability to your business:
Sell Potential Dead Stock Items At Discounts
Instead of waiting for inventory to become dead stock, proactively put them up for sale at discounted prices. Market trend data is enough to estimate what is selling now, what is likely to sell in the future, what will continue to be popular in the long run, and what will lose popularity eventually. For instance, holiday products typically vanish from the shelves in the weeks leading up to the D-day, but demands drop as soon as the holiday season is over. Rather than stocking up on items that may never sell, get rid of the excess stock by offering heavy discounts. It may not be profitable, but you can dodge a dead inventory situation.
Stay Updated With Market Trends And Forecasts
Do some market research and keep an eye out for trends and forecasts to help you decide on the products you should stock. Survey your current customer base and gather insights on what is trending among your buyer persona. With these insights, you can predict what products may perform well and stock up on those least likely to turn into dead stock. Leverage inventory software to come up with the best estimates for your business based on analytics reports and automated tracking.
Dead Stock Inventory Management: How To Turn Dead Stock Into Sales?
Controlling your inventory is crucial to leading a successful business venture. Given its importance, let us take a glance at some inventory-control strategies you could implement in your warehouse:
Sort Your Inventory By Importance
Organizing your checklists into priority groups will help you figure out which things you need to purchase more regularly and which are crucial to the business but may be more expensive and take longer to move. Specialists advise categorizing your inventory into A, B, and C categories. The A category contains more incredible things that you will need less. The B group consists of modestly valued things and flows out the doors slower than C items but faster than A items. Low-cost items with a high turnover rate fall into the C category.
Inspect Your Stock
Some firms conduct a comprehensive census once a year, while others conduct random inspections on their most popular items monthly or daily. Many people do all of these things. Make it a habit to personally measure your stock regularly, irrespective of how often it is done.
Examine Your Suppliers' Performance
An unreliable provider may harm your inventory. It’s time to act if your supplier is consistently late with shipments or under-delivering an order.
Discuss the concerns with your provider and determine the root of the issue. Then, be ready to change partners or cope with erratic supply levels and the risk of being out of merchandise.
Invest In Inventory Control Software
If your company is small enough, you may manually manage the first eight items on this list using spreadsheets and notes. However, if your firm expands, you’ll need to invest more time on stock than your firm or risk having too much inventory.
All of these activities are made more accessible by good inventory management software. Once you select a software package, make sure you know what you need, that it has the metrics you need, and that it’s simple to use.
Track In Batches
Batch tracking or monitoring is a quality assurance inventory control tool that allows users to organize and track material with comparable characteristics. This technique is beneficial for monitoring inventory obsolescence or tracing damaged goods back to their originating lot.
Use Continuous Inventory Management
Continuous inventory management essentially means counting goods. It’s the most basic method of inventory control, and it can be performed manually or with a digital database.
Use Manufacturing Lean
Lean is a collection of management methods you may implement in any industry. Its purpose is to increase productivity by removing wastage and non-value-adding activities from day-to-day operations.
Forecasting Inventory Based On Demand
Retailers should be conversant with sales forecasts as an inventory management method. The prediction of client demand is based on preliminary sales figures. It’s a projection of the goods or services a firm anticipates customers to buy in the future.
Utilize Cross-Docking
Cross-docking is an inventory control approach in which materials are unloaded directly into outbound vehicles, resulting in a JIT (Just In Time) shipment procedure.
What Is an Inventory Control System?
An inventory control system is a technology solution that maintains and tracks a company’s commodities across the supply chain. Procurement, shipment, acquiring, storage, and cancellations will all be managed using this platform.
The best inventory system will automate many manual operations. It will show you exactly how much stock you possess, where it is, and when you need to restock to maintain ideal stock levels.
Inventory Control Method Comparisons
Various inventory management approaches can lead to efficient inventory management. Some of the frequently used methods are:
The Just-In-Time (JIT) Method
Just-in-time inventory management is a Japanese inventory management technique. A corporation keeps only as much stock as it needs during the manufacturing or production process. As a result, there is no excess stock on hand, which saves money on storage, transportation, security, and other related expenses. More merchandise is ordered once the old inventory is ready to be refilled.
However, this is a slightly dangerous inventory management strategy because even a minor delay could lead to the loss of sales revenue that the business cannot fill. As a result, effective planning, an efficient provider, and prompt stock arrival are required to place fresh orders on time.
Model Of Economic Order Quantity (EOQ) Method
The EOQ inventory model concentrates on a company’s choice of how much stock should be purchased and when you should make the purchase. When inventory exceeds the minimum ordering level, it is reordered using this method. This inventory control method reduces the cost of maintaining and purchasing items when placing an order.
Material Requirement Planning (MRP) Method
MRP (Material Requirements Planning) is a method of inventory control. The manufacturers/producers order inventory using this method after considering the sales prediction. The Material Requirements Planning (MRP) system combines data from several organization sections that use stocks. After weighing the data and market requirements, a fresh inventory order is created.
Point Reordering Formula Method
The reorder method is a stock management strategy based on a company’s buy and sales periods, which vary by product. As a result, a reorder point is frequently higher than a safe inventory level to account for wait time.
Minimum Order Quantity Method
Minimum Order Quantity (MOQ) refers to a small amount of fixed stock that a provider is ready to sell. If merchants seem unable to meet a product’s MOQ, the supplier will not sell it to the business.
Inventory products that cost more to produce, for example, often have a lower MOQ than goods that are cheaper and quicker to deliver.
Dropshipping Inventory Management Method
Dropshipping is a type of inventory control fulfillment where a retailer does not maintain the items it sells in-store. Instead of picking an item from their inventory, a store will purchase it from a third-party provider and supply it to the customer. The vendor is never aware that we have touched the product.
LIFO & FIFO Method
LIFO and FIFO are two methodologies for calculating inventory costs. First in, first out, or FIFO, assumes that older merchandise is sold first. FIFO is an excellent method for keeping inventory fresh.
Last-in, first-out (LIFO) assumes that newer inventory is sold preferentially. LIFO helps to keep merchandise from spoiling.
Conclusion
An e-commerce store’s inventory is its lifeblood. Backorders are avoided, consumers are satisfied, and your firm is lucrative when you have the right products in stock. By streamlining and automating inventory control operations, optimizing your logistic cycle, and providing you with a real-time picture of stock levels, a robust inventory management system may help you save time and money.
Sign up today and LEAVE THE LOGISTICS TO US
Sign up, and we will get back to you within 24 hours to discuss what services would be best for your business needs. Or speak with us now and tell us what you need.
FAQs
ABC Analysis, Inventory Production Quantity, and Economic Order Quantity are the three inventory control methods.
The two ways to control inventory in storage are setting proper pre-order levels and opting for a sound inventory maintenance system.
You can manage store inventory by keeping track of inventory, auditing your list, prioritizing your inventory, and using technology that integrates well with your business.
The commonly followed inventory control procedures are getting rid of unsold stock, optimizing inventory, and prioritizing accessibility and location.
Store inventory refers to any lender’s inventory kept in a store to sell to consumers. Store inventory refers to the things for sale displayed in the contract’s timetable.