Blog
- All
- Business
- Outlook
- Operations
- Growth
- Case Studies
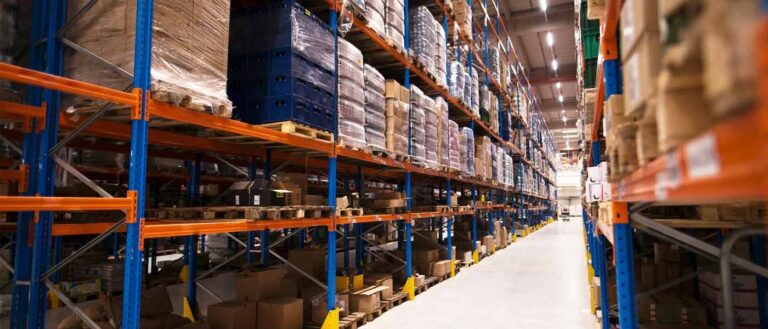
E-commerce in the GCC is growing, with millions of online shoppers and 39% demanding faster deliveries...
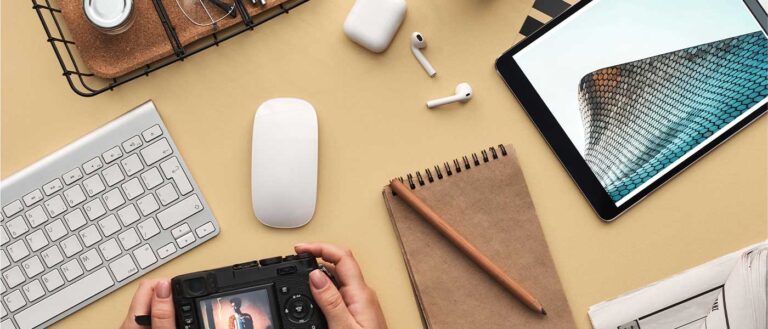
Did you know that the UAE’s e-commerce market is growing at a healthy rate of 6.02% and will reach US$10.11...
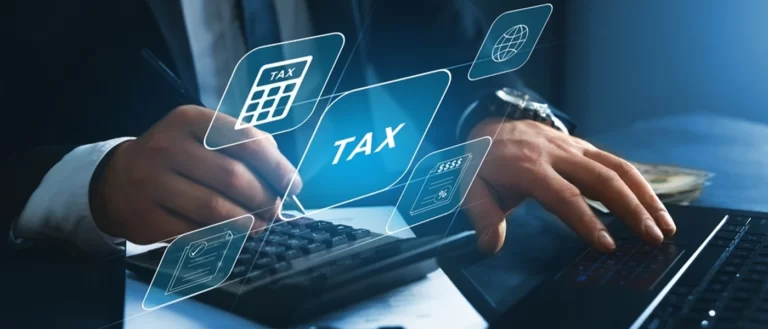
In 2024, UAE foreign trade soared to $817 billion, creating massive opportunities for e-commerce sellers...
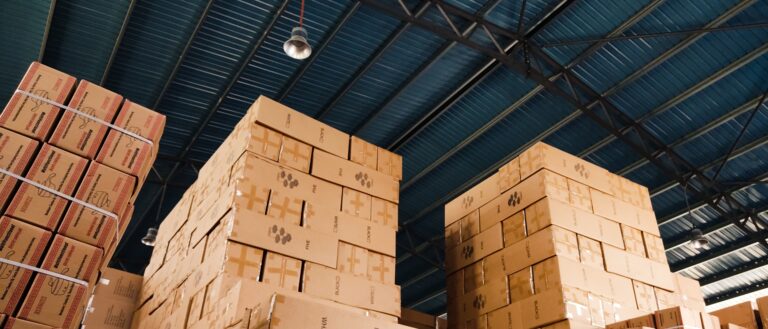
The UAE is a global trade hub, attracting businesses looking to scale and cater to a growing audience....
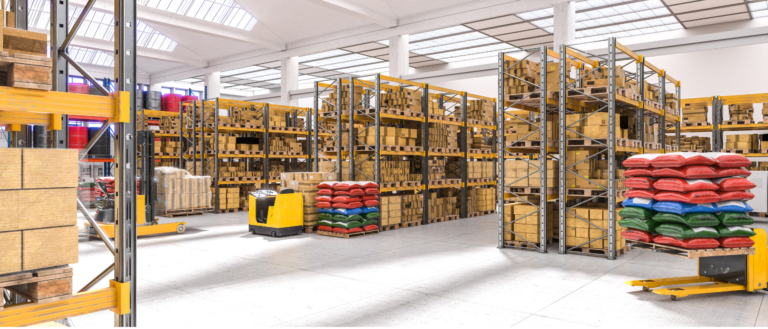
Sourcing products not made in China can help you build resilience amid trade uncertainties. Find out...
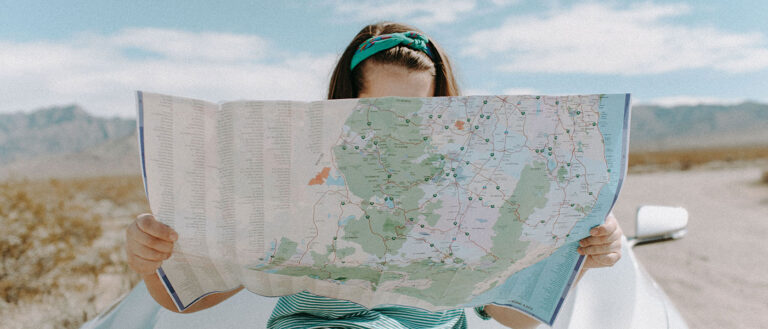
Find out how friendshoring helps e-commerce sellers build long-term supply chain resilience, reduce tariffs...
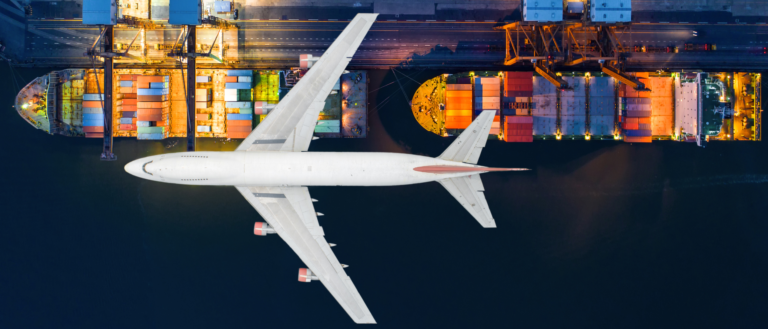
Did you know that the total shipping from China to the UAE increased by 24.5% between December 2023 and...
The holy month of Ramadan influences how consumers in the Middle East spend time and money on lifestyle...
Meet our client: Bed&Butter Founded with a passion for comfort, quality, and affordability, Bed&Butter...
No posts found
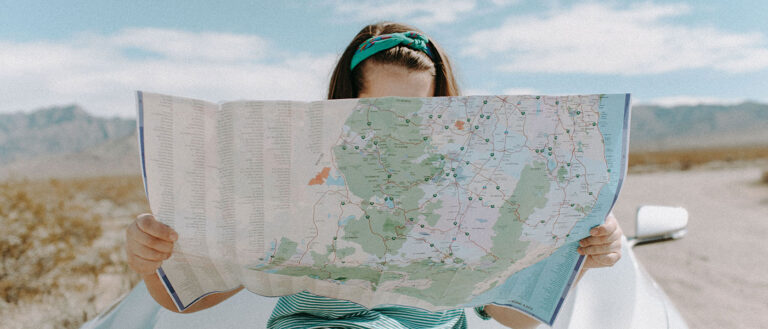
Find out how friendshoring helps e-commerce sellers build long-term supply chain resilience, reduce tariffs...
Understanding e-commerce trends is crucial for e-commerce, especially in an evolving market like Singapore....
Singapore’s e-commerce market is thriving, with consumers shopping online more than ever before. The...
Singapore’s e-commerce market is experiencing rapid growth and is currently valued at US $5.02 billion....
In 2024, Singaporeans are shopping online more than ever before. Approximately 62.8% of Singaporeans...
As the year draws to a close, mega-sale days get bigger and better. Combine that with the ber months...
The Singles’ Day sale is a shopping phenomenon that has transcended borders and revolutionised how Australians...
The second quarter of the year is when e-commerce lights up in Australia thanks to all the mega retail...
Running an e-commerce business requires you to wear many hats. You might be getting the manufacturing,...
No posts found
E-commerce networking events are the perfect opportunity to discuss trends, success stories, learnings,...
Across the world, there are over 9.1 million e-commerce companies.. Moreover, the e-commerce market has...
There are two practical approaches that companies choose in e-commerce: fast e-commerce and sustainable...
Being an extremely significant factor of any business, customer service is assistance that is provided...
Imagine sitting on your couch, scrolling through your favourite online store, and trying to decide what...
With the shift in consumer behavior towards shopping online, it now becomes a question of which social...
Rising popularity of e-commerce and social media marketplaces lead the way for omni-channel fulfillment...
The list below shows the implementation of consumer protection laws related to e-commerce among Southeast...
No posts found
Understanding e-commerce trends is crucial for e-commerce, especially in an evolving market like Singapore....
Singapore’s e-commerce market is thriving, with consumers shopping online more than ever before. The...
The Singles’ Day sale is a shopping phenomenon that has transcended borders and revolutionised how Australians...
Running an e-commerce business requires you to wear many hats. You might be getting the manufacturing,...
As the spooky festivities approach, Filipinos focus on the days before Halloween, All Saints' Day, and...
Halloween, a predominantly American tradition, has become popular in Australia. At the end of October,...
Stock Keeping Unit (SKU) rationalization is the process of identifying and removing underperforming products...
In today’s e-commerce world, ensuring speedy order delivery and customer satisfaction is key. As your...
E-commerce networking events are the perfect opportunity to discuss trends, success stories, learnings,...
No posts found
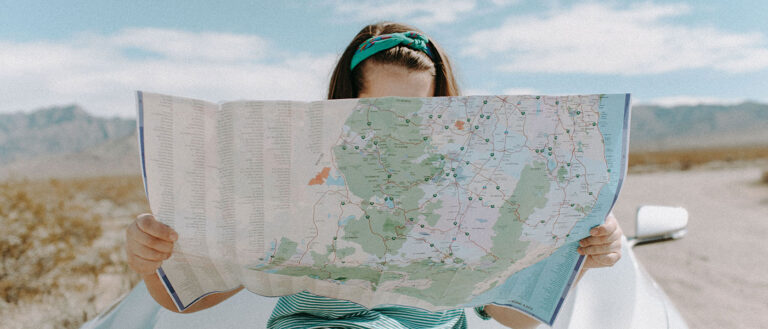
Find out how friendshoring helps e-commerce sellers build long-term supply chain resilience, reduce tariffs...
Understanding e-commerce trends is crucial for e-commerce, especially in an evolving market like Singapore....
The Malaysias e-commerce market is expanding rapidly, at CAGR of 14.32%. By the end of 2024, it is expected...
Singapore’s e-commerce market is thriving, with consumers shopping online more than ever before. The...
The Singles’ Day sale is a shopping phenomenon that has transcended borders and revolutionised how Australians...
The second quarter of the year is when e-commerce lights up in Australia thanks to all the mega retail...
Running an e-commerce business requires you to wear many hats. You might be getting the manufacturing,...
As the spooky festivities approach, Filipinos focus on the days before Halloween, All Saints' Day, and...
Halloween, a predominantly American tradition, has become popular in Australia. At the end of October,...
No posts found
Meet our client: Bed&Butter Founded with a passion for comfort, quality, and affordability, Bed&Butter...
Meet our client: Love Luggage Founded with a passion for combining style, durability, and functionality,...
Meet our client: Saipo Saipo is a skincare brand that sells vegan, cruelty-free, and clean products....
Find out how one of the country’s fast-growing dermatology clinics, DMD Skin Science, became a nationwide...
Meet our client: Four Little Monkeys Four Little Monkeys specializes in equipment for the early stages...
Meet our client: The Ayurveda Experience The Ayurveda Experience is reshaping modern health, wellness,...
2023 - it technically feels like yesterday, but the year that passed by has been a box of surprises....
Mama’s Choice is a healthcare brand based in Thailand focused on developing products tailored to the...
Cosmic Cookware is a kitchen companion brand that creates pans and accessories that not only look good,...
No posts found
Get the latest industry news, best practices, and product updates!
All Systems Go
Sign up, and we will get back to you within 24 hours to discuss what services would be best for your business needs. Or speak with us now and tell us what you need.